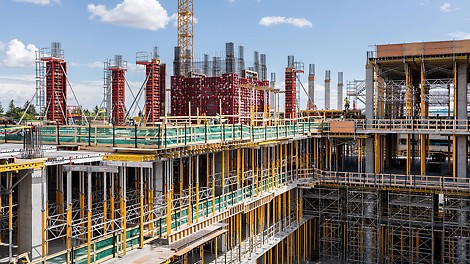
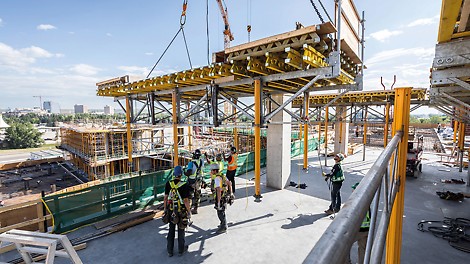
Download Press Release
The images in more detail
By order of the government of Alberta, a hospital, a day care centre and a state-of-the-art research laboratory are being constructed on an area covering a total of 185,000 m2. The aim is to offer patients groundbreaking cancer treatment and patient and family-centred care at the premises of the Foothills Medical Centre when the facility opens in 2023. This vision is symbolised by the highly unusual shape of the building: A child and an adult embracing each other and breathing as one. Once the project is complete, which is scheduled for November 2023, the building will consist of 18 storeys, 5 of them below ground level and 13 above ground.
A complex formwork and scaffolding solution from a single source
For the construction work, the customer is relying entirely on tried-and-tested PERI system solutions: Engineers from PERI developed plans to combine 14 different system solutions which have been tailored to meet on-site requirements. In addition to the most complex SKYTABLE structure ever executed and a state-of-the-art VARIOKIT VRB solution, a total of more than 15,000 m² of slab formwork, 4,000 m² of wall formwork, extensive scaffolding material and more than 12,000 MULTIPROP and 9,000 PEP props will be used over the course of the project. In a world first, TRIO TRS 120 columns will be used on the construction site. These columns will be used alongside the TRS 90 columns, enabling the construction company to meet column size requirements.
Atypical building structure with varying storey heights
The first stage of the build, which was completed in June 2019, comprised the construction of the five-storey underground garage, which covers a total area of around 100,000 m2 and consists of a total concrete volume of 68,000 m³. The characteristic feature of the parking area is its complex structure with storey heights that range from 3.5 m to 7 m. The PERI engineers used SKYDECK slab formwork to achieve this. The lightweight components allowed the site personnel to conserve energy during the construction process. At the same time, it was possible to keep shuttering times to a minimum. The drophead system facilitated early striking, meaning that elements could be removed after a comparatively short period of time and re-used for other concreting sections.
For the above-ground section of the building, over 400 assembly and overview drawings have been produced in collaboration with the client in order to develop the most complex SKYTABLE project structure ever implemented: A total of 247 slab tables consisting of 218 different designs are being used for the Calgary Cancer Centre construction project. On account of the limited assembly space on site, these are being pre-assembled and delivered just-in-time. They will then be connected to the pre-assembled girders on site.
Just like the planning phase, the design of the VRB solutions is one of the many challenges posed by this project. A total of 36 22 m-long VRB girders will be assembled to form 18 truss girder packages with platform units. The cantilever begins on level 4 and extends from the building by around 9 m to enable casting of the slab above. By carrying out structural calculations, it is possible to prevent system overload caused by tensile, compressive and bending forces, meaning that another challenge could be successfully overcome.
BIM – creating reality from virtual reality
The planning phase of this enormous project was time-consuming: For about a year, PERI engineers worked meticulously to establish the optimum approach to coordination, implementation and logistics to maximise the efficiency of the construction site procedures. With the aid of BIM (BIM = Building Information Modelling), a 3D model was created. In this way, the individual assembly steps, particularly with regard to the VRB solution, can be presented to the construction workers in a visual and comprehensible manner. It is also possible to use the 3D model to calculate the optimal area covered by the VRB truss girder packages during disassembly at the constricted construction site. The team can also make use of the 4D timetable, an additional tool that provides support with sequence planning at the construction site and clarifies the assembly and disassembly processes for the VRB truss girder packages.