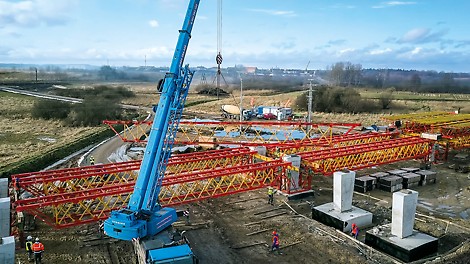
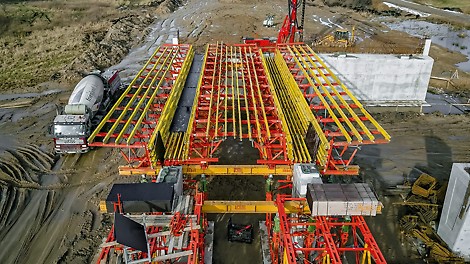
Download Press Release
The images in more detail
The 160 m long M-8 road bridge forms the core of the 12 km long by-pass which circumvents the town of Szczecinek. As part of the S-11 highway expansion project, the bridge crosses the wetlands surrounding the Wilczy Canal, and features two lanes in each direction. Difficult ground conditions required a non-commonplace shoring solution that could not be implemented using standard systems due to the large spans and high loads. PERI provided an efficient solution to meet these requirements based on the VARIOKIT Engineering Construction Kit, which included planning, pre-assembly and delivery as well as comprehensive project support.
Large spans solved within the system
The implementation plan provided for two independent bridge superstructures complete with a pre-stressed, twin-webbed T-beam cross-section. The best solution proved to be a shoring structure with sectional span widths of 20.50 m and 25.50 m, placed on the foundations of the fixed bridge supports and without intermediate supports in the bridge segments.
After taking into consideration various technical solutions, the contractor decided in favour of the version proposed by PERI using VRB Heavy-Duty Truss Girders on shoring tower frames. This support structure on the basis of the VARIOKIT Engineering Construction Kit convinced Eurovia Polska S.A. in particular due to the low weight, modularity of truss girder segments as well as the easy and quick assembly of the fitting pin connections. The VARIOKIT Engineering Construction Kit is predestined for applications in bridge construction – because when using the versatile core components, standardized system components and simple fitting pin connections, it is possible to systematically erect heavy-duty shoring towers and trusses with wide spans for bridge construction. The VRB Heavy-Duty Truss Girder, for example, was developed for spans up to 40 m and a permissible bending moment of 3,000 kNm.
Fast construction progress thanks to pre-assembly and fast modification work
For forming the superstructure consisting of bridge beams and adjoining carriageway slab, the team pf planners combined VARIOKIT formwork units with VARIO GT 24 Girder Wall Formwork components. The respective sections of the two parallel superstructures were alternately concreted whereby the formwork and shoring were placed in an offset position from one bridge segment to the other.
As there was no suitable fixed assembly area on the construction site, PERI ensured that pre-assembly of the truss girders – in 12.50 m long segments – in the PERI assembly hall was completed on time. Subsequently, several material packages consisting of braced birdcage scaffolding complete with truss girder frames were delivered to the jobsite just-in-time. Once there, the construction team connected the units to form pairs of truss girders with a total length of 20.50 m and 25.50 m respectively and mounted them on the VST Shoring Tower Frames. In this way, the truss girder assembly could be carried out at the same time as the erection of the shoring towers. This reduced both the required on-site material requirements which saved on material and storage costs as well as time. In order to accelerate the final assembly, PERI also delivered pre-assembled formwork units to the construction site. The PERI formwork erection process ensured accurate assembly and punctual scheduling.
Cross-sectionally, the shoring solution consisted of six VRB Truss Girder levels. Three trusses each were connected to each other and braced in order to carry the superstructure formwork of a bridge beam. The VRB Truss Girder is always comprised of different load and length-optimised frame types which allow infinitely variable spans by means of corresponding combinations. For the Szczecinek bridge, the modules of the respective assembly variants were selected to ensure that any adaptation to suit the different lengths of the middle bridge sections and the edge segments was carried out quickly and easily. PERI UP Stairs integrated into the solution always ensured safe access to the superstructure.
Formwork – Scaffolding – Engineering – everything from one source
PERI not only took over the technical processing and static calculations of the overall solution for the project. PERI engineers supported the construction team throughout the entire building process with on-time logistics and on-site project support. In this way, all requirements could be met as well as ensuring that the tight construction schedule was maintained.