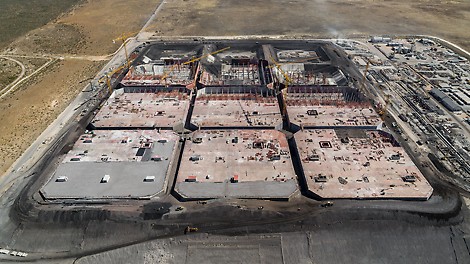
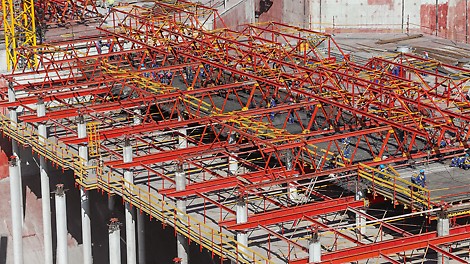
Download Press Release
The images in more detail
The Saldanha Bay site in South Africa in particular makes the tank storage facility an interesting proposition for investors. Located between the Atlantic Ocean and Indian Ocean, the OTMS project provides quick access to markets in America, Europe and Asia. Therefore, the decision was taken to go ahead with the million-dollar crude oil storage project in an area north-west of Cape Town. Over a three-year period, a total of 1.5 million cubic metres of earth was excavated and moved while 150,000 cubic metres of concrete was used in construction operations.
Enormous challenge – unconventionally solved
Realising the 110 m x 110 m tank storage facility slabs at heights of 17 m was not economically feasible using standard methods. In the early phase of the project, the clients of WBHO had already decided to collaborate with PERI and jointly search for the optimum building method. Instead of a conventional slab formwork solution, the engineers designed a construction version borrowed from bridge building using formwork carriages. In the process, the table-like slab formwork was supported by the project-specific VARIOKIT framework super-structure. This construction method using formwork carriages allowed the slab formwork to be lowered just one day after concreting operations and moved 8 m to the next section. The high load-bearing capacity of the VARIOKIT system provided the necessary support for the concrete slab until it had reached sufficient strength. Using only seven formwork carriage units per tank, each casting segment crane-independently realised 880 m² of slab area per storage tank in regular 5-day cycles.
What does not fit is made to fit
The concrete slabs of the tanks are supported by a total of 2,400 concrete columns with diameters of 50 cm or 60 cm respectively which are arranged using a chequered layout with standard distances of eight metres within the tanks. Their execution resulted in several problems: due to the height of the columns, the usual lead formwork proved to be too unstable. In addition, the 17 m high formwork had to be cleaned while still in a vertical position and subsequently oiled for its next use because it was simply not possible to lay it on the ground because of the lack of space and time.
Together with the building contractor, WBHO Construction, PERI therefore developed a 1:1 prototype of the formwork and carried out an extensive range of testing in advance of the actual construction work. The result of the detailed test phase: formwork halves of the SRS circular column formwork braced with a lattice framework. Thanks to the use of additional platforms, they could be cleaned and oiled while still vertically positioned. This hitherto completely new approach for realising concrete columns turned out to be extremely effective. Consequently, up to 40 concrete columns per week could be constructed in parallel on the construction site.
Project-specific TRIO solution keeps the costs under control
For constructing the vertical tank walls, the contractors opted for a special solution with TRIO Panel Formwork elements. The client's specification demanded the use of 4 mm thick steel formlining instead of the customary plywood formliner. In order to keep the investment costs under control, spacers were welded to the rear of the formlining before they were riveted to the TRIO panels. As a result, the client was provided with a solution whereby the frames could be obtained from the PERI rental park while only the formlining had to be purchased.
By supplying a special lifting beam, large-sized units of up to 75 m² could be moved with a single crane pick. Using a total of 3,300 m² of TRIO, not only the tank walls but also all the walls of the pumping station as well as the concrete casing of the pipelines were quickly and cost-effectively formed.
Building Information Modelling optimises the construction process
During the construction phase, project participants were continuously able to draw on a large amount of relevant information and without any delay. 3D models simplified on-site coordination and facilitated fast and reliable execution and control processes. The information could be retrieved at anytime and anywhere on the jobsite, which made it possible to work through existing checklists without any problems. This ensured optimised workflows and smooth transitions between the construction cycles that ultimately benefited the construction process of the entire project.
On the construction site itself, PERI project coordinators were always available to assist the contractor with the benefit of their many years of accumulated expertise and knowledge. In addition, the PERI supervisor briefed site personnel as and when required regarding the correct and safe handling of the systems used along with project-specific execution methods.